BMA Automation completes process control system for the Agrosnabsakhar factory
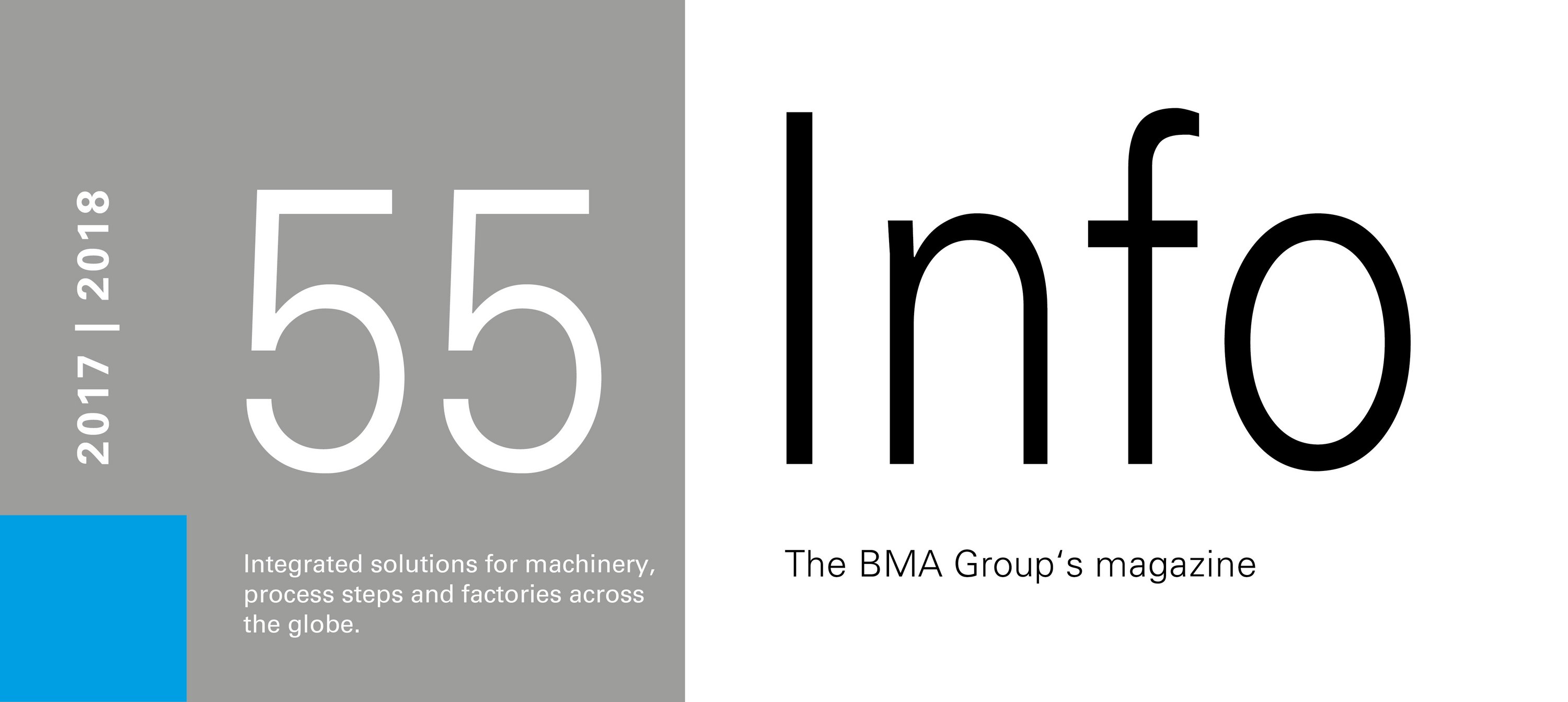
01.07.2017
The next chapter in a success story
BMA have maintained a fruitful partnership with the Agrosnabsakhar sugar factory, based in Elets in Russia, since 2010. Our subsidiary BMA Automation has played a key role in the factory conversion.
After BMA had supplied a number of plants to Agrosnabsakhar in previous years, BMA Automation implemented a process control system there in 2015. Our customer had high expectations of the system’s bene t and the result; these were fully met during the 2015 / 16 campaign. What came next was a follow-up order for BMA Automation, for automation of all stations in the process control system.
Elets II: automation continues
Last year, it was time for the biggest step of the factory conversion: automation of the new extraction plant, the process water treatment plant, the pressing station, the gypsum plant, all seven falling- lm evaporators (four of them new units), the new vertical cooling crystalliser, the new sugar packing station, the old extraction plant, and the treatment plant for beet residue and leaves.
The scope of supplies from BMA Automation also included integration into the process control system of a juice purification station from another manufacturer and the lime kiln. Last but not least, the centrifugal station, comprising four B-type and three E-type centrifugals from different years, had to be integrated. We were also given responsibility for assembly and installation of the complete switchgear, of a total length of 50 metres.
Factory acceptance test more than pays off
Once more, success was guaranteed by factory acceptance testing (FAT) using the SIMIT software, to verify and optimise processes and interactions between components in a realistic environment. This was the rst time we also used FAT as a training tool: a team of shift fore- men and the production manager from Agrosnabsakhar combined factory acceptance with a training event. It meant that our customer’s staff were under no time pressure to familiarise themselves with the system, well before the start of the campaign. This paid off later, in Russia: the shift foremen shared their knowledge and were able to provide support to the plant operators.
Readers with knowledge of this field will realise what the reconstruction of such a large number of plants entails. And their sheer number was not the only challenge. Installation of the new mechanical and Central control room electrical systems for the plants had to be completed simultaneously. BMA Russia deployed a large team to the construction site for assembly, plus 15 experts for commissioning.
BMA hardware professionals ensured faultless connection, instrumentation specialists set the measuring ranges, and programmers brought all efforts together. During the critical commissioning stage, our customer even organised a shuttle bus to take all these experts to and from the construction site. Thanks to the high level of commitment from all project participants – the Agrosnabsakhar sugar factory, BMA Russia and BMA Automation – the 2016 / 2017 campaign got off to a successful start.
More capacity, more efficiency
The outcome: after the reconstruction and upgrade projects of recent years, our customer has now almost doubled his former beet processing capacity of 5,500 t / d. And the capacity increase is not the only bene t. With the use of state-of-the-art equipment, efficiency has improved considerably. Completion of the sugar silo will end this period of conversion and growth.
The two automation projects are impressive evidence that the step-by-step reconstruction of a sugar factory is indeed possible – within a short time even. For the Agrosnabsakhar sugar factory, its trust in the expertise of BMA Automation and the willingness to invest in a state-of- the-art process automation system have certainly paid off. In terms of automation technology, it has secured its leading position in the Russian sugar sector.
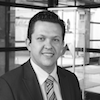
More about BMA Automation