A special drying system for sewage treatment
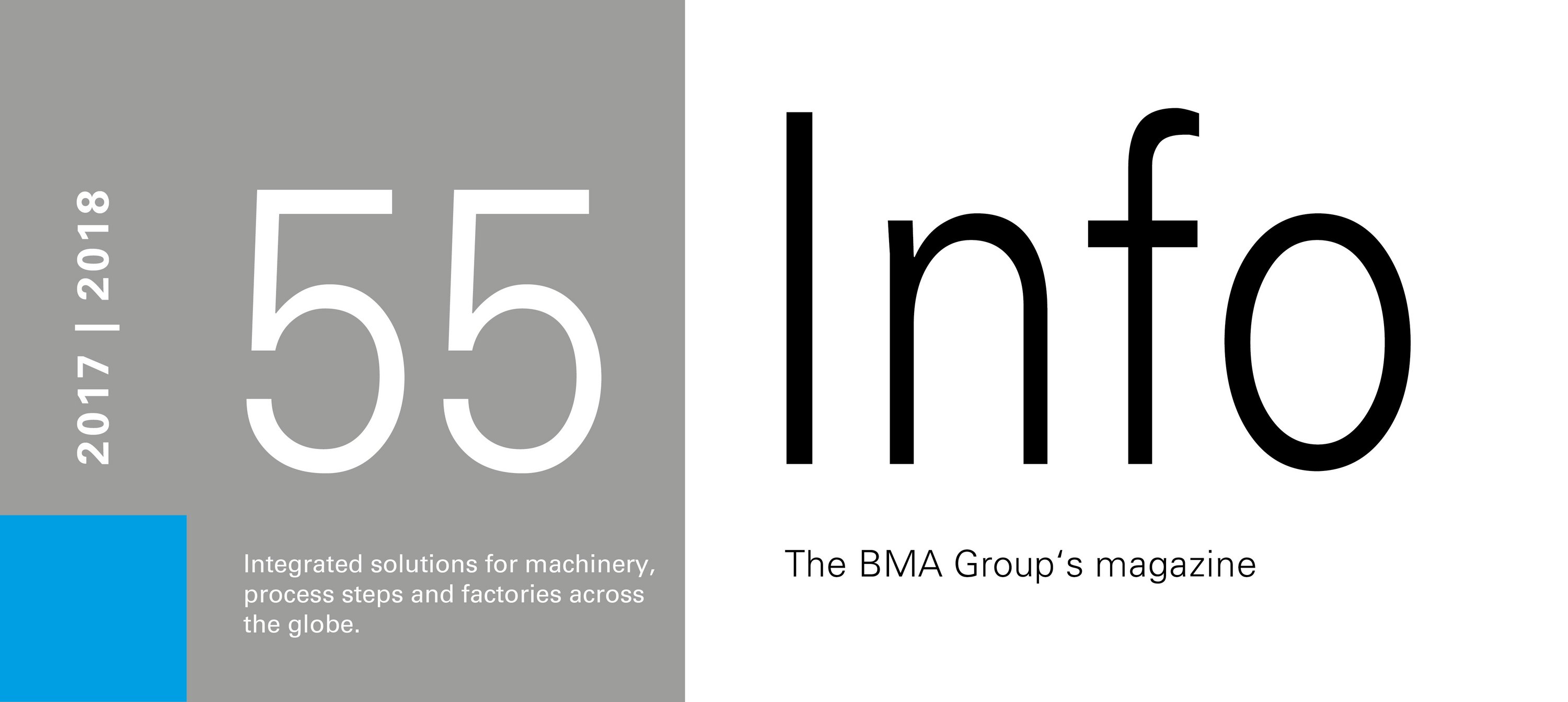
01.07.2017
Steam power
It takes up very little space, saves up to 95 percent of energy for drying, works fast and produces no smells: the drying of sewage sludge using superheated steam. Beet sugar factories have been relying on this technology for some time, but for sewage treatment plants, it is a new approach to sludge disposal and capacity extension.
The disposal of wet sewage sludge is expensive, except when used in agriculture, which is why treatment plants opt for drying the sludge. The downside of this approach is that only a very small part of the energy used for traditional drying methods (with a disc, belt or drum dryer) can be recovered. As with the standard drum drying of beet pulp, there are no potential consumers for large volumes of hot and humid air.
Unique testing facility for drying sewage sludge
What treatment plant operators and waste management companies therefore badly need are different drying methods – such as steam drying above atmospheric pressure. This method permits the recovery of energy from the released steam with vapour condensation; in addition, the vapour ingredients will be available in liquid form. So BMA have been at work since early 2016, in real-life operating conditions, in a pilot plant-scale testing facility that is unique in the world, to develop concepts for drying sewage sludge using superheated steam in a fluidised bed.
The timing has been perfect. With the amendment to the regulation on sewage sludges and fertilisers, due to take effect in Germany this year, the country’s treatment plant operators are feeling the pressure. They will have to come up with new concepts for the use of sewage sludge, as the low-cost option of applying it to farmland will no longer be available from 2029.
Germany alone produces around seven million tons of wet sewage sludge annually in its more than 10,000 treatment plants. Most of this will have to be dried in future – partly to achieve the legally prescribed recovery of nitrogen and phosphorus. Sewage sludge in Germany contains roughly 60,000 tons of phosphorus, a much needed mineral fertiliser, about a third of which is used in agri- culture. To recover the phosphorus, it has to be upgraded: sludge dewatering -> drying -> mono-incineration.
Thanks to the technological advances of recent years, sludge dewatering today yields a dry substance content of up to 0.35 kg per kg of overall weight (kgDM/kg), or 40 percent more than previously. No such leaps in technology have been achieved in the drying of sewage sludge. This is partly due to the aws of conventional dryers, such as odour emissions, the risk of res or explosions and the problem of energy use, as well as the final moisture content of the sewage sludge, its so-called “sticky phase”, and the space needed for the equipment.
A closed drying system has many benefits
The solution to these problems is a steam dryer built as a pressure vessel with a fluidised bed. The pressure can be maintained only when the dryer is closed. This automatically results in an odourless process, which is also oxygen-free, thanks to the steam atmosphere. There is no risk of oxidation, res or explosions in the dryer. Because of the high temperatures during drying, both the condensate and the solids (> 0.95 kgDM / kg) are sterile.
The use of superheated steam reduces drying times compared to hot air drying. This in turn shortens the retention time of the sewage sludge in the dryer, which permits use of a machine with a smaller footprint. On an area of just three metres in diameter, a continuously operating fluidised-bed dryer can produce two tons per hour of low-dust, coarse product with a consistent dry substance content.
To achieve this, sewage sludge with a dry substance content of between 0.25 and 0.35 kg per kg of total weight is separated into particles – before the sticky phase – and gently dried in the fluidised bed to a final moisture content of 0.95 kgDM/kg. Fluidisation prevents agglomeration of the particles and caking on the walls. The sticky phase then has no impact on the drying of the sludge.
The water contained in the sewage sludge is converted to heating steam with a high level of energy, so the dryer becomes a steam generator. A by-product is dried sewage sludge. This reduces the cost of sewage sludge disposal while at the same time increasing its phosphorus content.
Effortless energy saving
The main product, vapour, still contains 95 percent of the drying energy used. Where does this energy come from? A treatment plant has many possible energy sources: co-generation plants, the thermal use of part of the sludge gas, and, ideally, incineration of the dried sewage sludge.
This means that less electricity is produced, a disadvantage that can, in a first step, be offset only by secondary benefits such as a small footprint, no emissions and lower disposal costs. But the bene t of steam drying is far greater if the vapour (150 °Celsius at 4 bar) is used in the treatment plant – and there are, in fact, several options available: disintegration of excess sludge or organic waste, ventilation of the aeration tanks, evaporation of highly contaminated wastewater, pre-drying, steam stripping, or district heat, to name but a few.
Through highly efficient cascaded condensation of one or several heat consumers, the energy becomes available again, so it can be reused and CO2 emissions reduced. In addition, some of the processes can increase the volume of sludge gas by up to 30 percent while reducing the sludge volume. As a result, new plants can be of a smaller size and the capacity of existing plants can be increased.
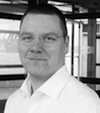