The benefits: less energy use and higher output.
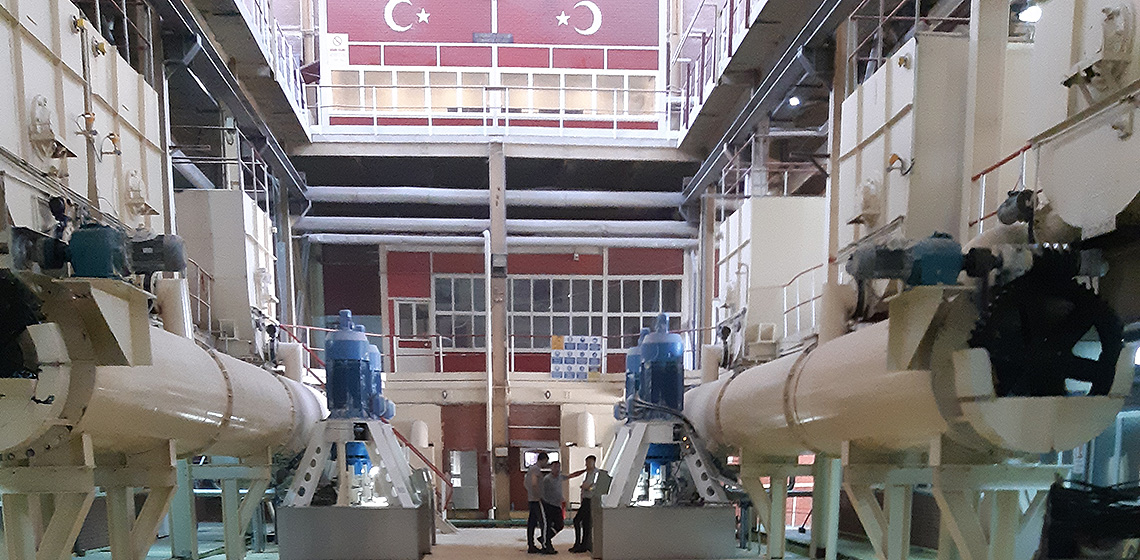
01.07.2021
BMA supplies E1810 centrifugals to sugar factories in Turkey
Kayseri Şeker Fabrikası A.Ş., one of Turkey’s largest sugar producers, has been a BMA business partner since 1955. Now a new chapter has been added to our shared success story, with a project for upgrade and capacity extension of the Turhal sugar factory. BMA also carried out work for the Turkish Safi Holding.
New BMA centrifugals for the campaign
Kayseri bought the Turhal sugar factory, which currently has a processing capacity of 8,000 t/d, as part of the privatisation of the state-owned Türkşeker. Once again, as in the upgrades of the Kayseri and Boğazlıyan sugar factories, Kayseri Sugar chose BMA as their partner. First in line for replacement was the centrifugal station. The factory has recently started to use four batch-type E1810 centrifugals from BMA, which have replaced the old machines. Last year, we successfully completed the centrifugal project at Turhal – just in time for the campaign, which starts in September.
E1810 centrifugals for high energy savings
The Çorum sugar factory, bought by Safi Holding as part of the privatisation of Türkşeker, has benefited from the same exchange. In an upgrade and capacity extension, 18 old centrifugals have been replaced by four state-of-the-art batch-type E1810 machines from BMA. One benefit are considerable energy savings: while the old machines together had a motor power of 1620 kW, the new E1810 centrifugals have a total installed capacity of only 800 kW.
Coin test proves: centrifugals from BMA have low vibrations
At the Çorum sugar factory, the famous coin test for batch centrifugals from BMA was a success. In this test, a coin is placed upright on the cover of a centrifugal in operation. From filling to discharging, the coin does not fall – proof that BMA machines have low vibrations and oscillations in operation.
E1810 centrifugals for a trouble-free campaign
Factory officials list the many benefits of the new centrifugals: low energy consumption, minimal operator input, more output, zero malfunctions during the campaign, very low annual spare parts cost, zero sugar leakages, and almost no vibrations. All work – from engineering to manufacturing, construction and testing, and to commissioning and training – was completed by the sugar experts from BMA AG