Development of hardware is a giant leap forward for BMA towards a networked sugar factory
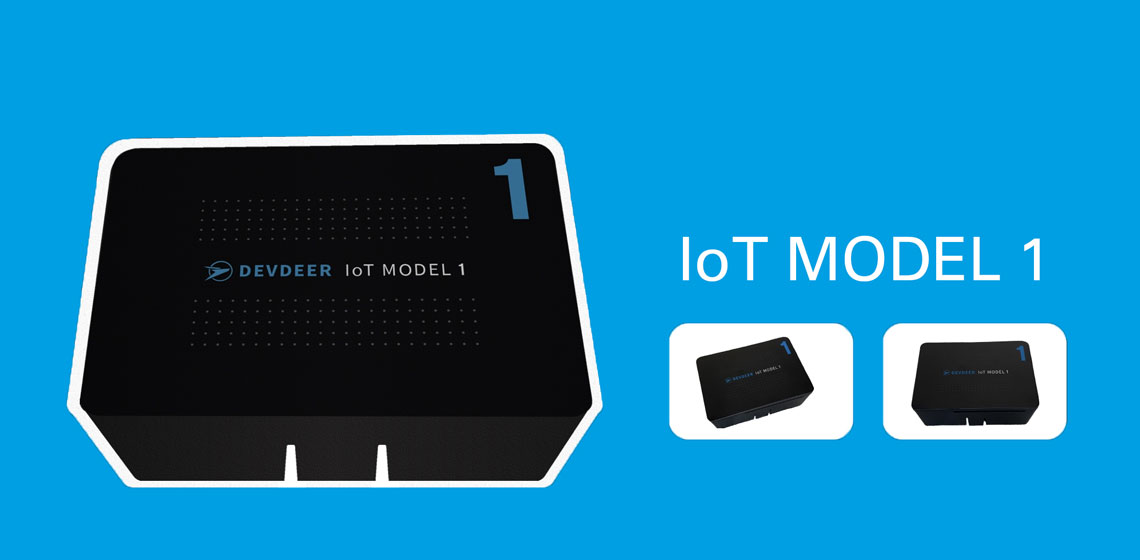
01.07.2021
Digital services for the sugar industry
BMA has been working on its digitalisation strategy smart4sugar for a digitally networked sugar factory since 2018. The aim is to make machine and production data available at any time and from anywhere in the world, tapping unused potential and increasing a factory’s efficiency. Our approach has been to develop a proprietary hardware, as an interface to the Microsoft Azure cloud. In this interview, Thorben Förster (Head of IT at BMA AG), Kristin Odörfer (Senior Manager Digital Sales at BMA AG) and Kevin Heyland (partner at DEVDEER GmbH) talk about the current status of development of the digital sugar factory, about the next steps – and why feedback from customers in the sugar industry is so important. BMA has been working on its digitalisation strategy smart4sugar for a digitally networked sugar factory since 2018. The aim is to make machine and production data available at any time and from anywhere in the world, tapping unused potential and increasing a factory’s efficiency. Our approach has been to develop a proprietary hardware, as an interface to the Microsoft Azure cloud. In this interview, Thorben Förster (Head of IT at BMA AG), Kristin Odörfer (Senior Manager Digital Sales at BMA AG) and Kevin Heyland (partner at DEVDEER GmbH) talk about the current status of development of the digital sugar factory, about the next steps – and why feedback from customers in the sugar industry is so important.
Interview partners
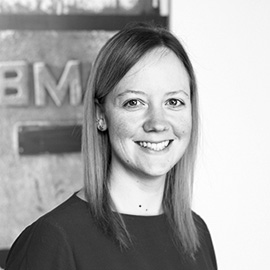
Kristin Odörfer is Senior Manager Digital Sales at BMA and acts as the interface between BMA Management, Sales, IT and development contractors. She heads the smart4sugar project.
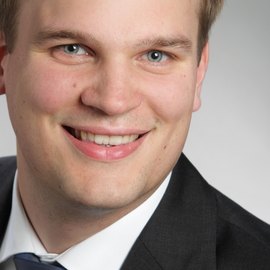
Thorben Förster heads the IT department at BMA, coordinating and planning our digital activities, such as the introduction of SharePoint.
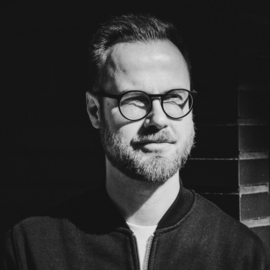
Kevin Heyland is a partner at Magdeburg-based DEVDEER GmbH. As the proxy product owner, he acts as the interface between customer product management and project management.
What’s at the root of the idea of creating smarter devices and machines?
Förster: For several years now, the market has been in an upbeat mood over the networking and digitalisation of machines. BMA saw this trend and has used it in the development of machinery and equipment. And that has evolved into a strategy. Part of this strategy is the creation of a digitally networked sugar factory in the near future. BMA decided as far back as late 2017 that we would move in that direction.
Odörfer: We’re doing it not just for ourselves, but above all for our customers. It’s important for them to be able to collect and analyse data. Which is why we decided to put our customers’ needs first. As a major partner of the global sugar industry, BMA is expected to address topics like that.
Heyland: There’s more than one way of creating smarter devices and machinery. Digitalisation is a huge field. Which makes it all the more important to look at the needs of the market regularly, and, if necessary, update and improve your strategy. We are aiming for maximum agility in this respect. It is both an enormous challenge and a great opportunity for mechanical engineering to align hardware development processes to the agile rhythms of software development.
Why does BMA need a gateway for smart.monitoring?
Odörfer: Simply put: because we want to transfer machine data. A gateway forms the interface between the machine and the cloud. It either has an integrated SIM card, or it is connected via the LAN at the production site.
Heyland: Particularly the digital service smart.monitoring will only work if live machine data from around the globe can be transmitted to the cloud. You could say that the gateway is the core of smart.monitoring. Remote access to data is important in cases where a service engineer from BMA can’t be on site because of travel restrictions such as we’re seeing currently in the global COVID-19 pandemic.
Was it difficult to find a suitable gateway on the market?
Förster: Yes, it did turn out to be a problem finding a gateway that could act as the interface between our machinery or device and Microsoft Azure.
Heyland: For the implementation of the defined specifications, you need an “out-of-the-box” gateway that you can simply connect, plus it has to be perfectly tailored to the features of the Microsoft Azure cloud. Machine data are processed in the cloud and then sent to be displayed in smart.monitoring. No ready-made gateway offers the necessary range of features for that. Which is why many devices today are not sufficiently compatible with Microsoft Azure – or they don't meet our requirements.
What exactly were you missing?
Förster: In a nutshell, we were looking for an interface that would permit direct integration with and control via Microsoft Azure. None of the software and hardware products on the market met those requirements. The crucial issue is that we want one device that permits both data transfer and device management. And we didn’t consider the security levels offered by standard gateway providers adequate either. We aim to offer our customers maximum security.
Odörfer: Another major requirement that wasn’t met was data compression. A considerable number of data packages are sent via the interface, which affects the bandwidth of the connection. And none of the devices tested had the desired compression function.
Heyland: Plus, we have to ensure reliable data transfer, wherever data are sent from. BMA installs large-scale plants for the sugar industry around the globe. And although the infrastructure for data exchange may not have the same high standards in every country, it still has to work everywhere.
So what conclusion did you reach after all your investigations?
Förster: We tried out various devices, but none of them met all our requirements. So it took us almost two years to establish that the devices available on the market would not be of any help. A situation that we were not at all happy with.
And what was the solution?
Förster: Over the course of these two years, we gained some real expert knowledge – so the problem hasn’t held us back, but in fact brought us forward. We decided to develop and build our own interface – that was our solution.
Heyland: In the end, it was much quicker to develop and implement BMA’s own solution. We started work in May 2020. Together with BMA, it took only a few months to develop a device that was ready for the market. Although we are software developers, we decided to develop the hardware as well, designing a device and building it. Even at the early orientation stage, DEVDEER proved to be a reliable partner for BMA. Because the development of a gateway from scratch is never a risk-free undertaking. The hardware has now been seamlessly integrated with the plants from BMA, which permits plug and play, meaning that there is no need for lengthy configuration; you can simply connect the device and start using it. In addition to developing the software, we also decided to build the gateway ourselves.
Odörfer: Over time, BMA has gained a range of specialist skills. By developing a gateway in collaboration with DEVDEER, we have created an interface that enables data exchange with the Microsoft Azure platform – another field where we are leading. And the smart4sugar platform strategy reflects that: we work with a single system rather than a number of different platforms.
What were the main steps in developing a gateway for worldwide deployment?
Förster: It took several steps, both on the software and hardware side. The initial basis and subsequent developments were achieved with the help of the developing team from DEVDEER. Next came the hardware specifications: certification, integration of SIM cards and much more. We split the project into two parts. One was communication between the gateway and the machine’s PLC; that task was completed by colleagues from Automation. DEVDEER were in charge of the integration and communication with the Microsoft Azure cloud, including visualisation of a dashboard for end customers. That process took two months.
What’s the current status?
Förster: We have now developed a second level gateway model. And we are continuously improving software features. All feedback that we receive about devices in use is implemented in the development process.
Odörfer: We’ve gone live with the product and are in close contact with our first mover customers. At the moment, we’re keeping a close eye on smart.monitoring user behaviour, to learn from these experiences.
Heyland: Looking at the smart.monitoring service today, I think we have achieved a lot. Dealing with the complexity, which was challenging from the start and still is, is a huge task that is nowhere near finished. Software development is a continuous process. We continue to work very closely with Research and Development at BMA, aiming to obtain even more accurate and reliable data for the dashboard. For BMA, two years is probably a very long time for a software development, though for us as software engineers, it’s not unusual. Particularly when such a project grows and matures with real user feedback. The smart4sugar project is a key project both for BMA and for the sugar industry as a whole. It comprises several subprojects, and the smart.monitoring dashboard is just one component. Initial feedback has been very promising and encouraging; it shows us that we’re on the right path.
What are your plans for the future?
Odörfer: We’re planning to create an online customer portal that will serve as a hub for all digital services such as the online shop or a configurator, and for contract data. There are also plans to add more equipment to the network. So in future, smart4sugar will be used not only for centrifugals, but cover all machinery and equipment in a sugar factory.
Heyland: This is an important time for smart.monitoring, as we’re receiving valuable feedback and data from customers, opening up a wealth of potential. Over the past months, the focus was on implementing remote services, so BMA customers would be able to make independent and informed decisions and act, despite travel restrictions and lockdowns. Some major planned features will also depend on factors other than a purely software development context. Existing systems will need to be updated or replaced, to connect them to smart4sugar; sources of digital revenue need to be handled; and an agile and digital transformation of procurement, logistics and controlling processes will have to happen. So there is plenty left to do. And that’s good.
Thank you for your time!