In recent years, automation has gradually found its way into manufacturing. It has revolutionised the way in which machinery, plants and equipment are produced, also for the sugar industry. At BMA, the introduction of two welding robots was a crucial step towards optimising production processes and improving the work environment for employees. “Our two robots have proved invaluable in supporting our work”, says Deniz Bagci.
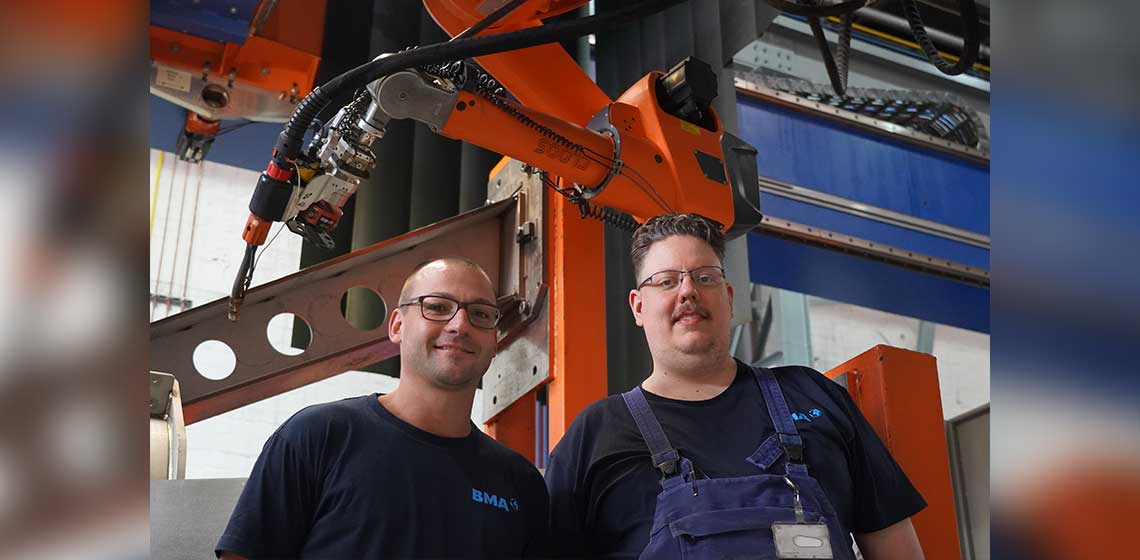
Automation in action: welding robots optimise production and make for a better work environment at BMA
Innovative technology for greater efficiency and a smaller workload
Welding robots for greater speed and precision
Deniz Bagci has experienced the transformative effect of automation first hand. When BMA expanded its machine inventory to include a fully automatic robot in October 2016, 39-year old Bagci became its first operator – and the first to experience a considerable improvement in his daily work routine. The robot completes all welding tasks quickly, with precision, and completely independently, he says. The process couldn’t be simpler: “Install it, set it up, let it run”.
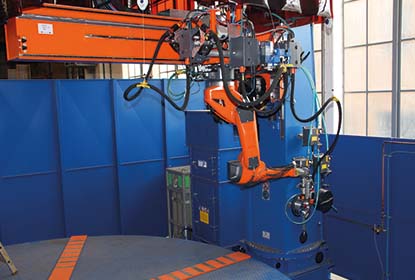
Use of robots in tank construction at BMA
A 10-axis robot from the well-known robot manufacturer Cloos is used in tank construction at BMA, playing a key role in the production of components for batch pans. In the so-called calandria, it welds hundreds of tubes to the boreholes in both tube plates. “This welding task has a high repetition rate of thousands of metres every month, which is why it made sense to have it done by a robot,” explains Deniz Bagci. Many of our tanks for the sugar industry have diameters of several metres – a special challenge that a robot must be designed for, such as with a 30 t welding turntable.
Automation as a solution for the shortage of skilled workers
Integrating this robot into production has considerably improved our employees’ everyday work. Instead of dealing with repetitive and physically demanding tasks that previously required the full attention of two people, our welders can now focus on more complex and sophisticated welding jobs – putting their skills to better use and furthering their professional development. It makes BMA a more attractive employer for qualified workers and helps to retain them – a crucial advantage, as skilled employees are increasingly difficult to find in the labour market.
Robotic and manual welding
Deniz Bagci, who joined BMA 22 years ago and is today the deputy welding supervisor, says: “Manual welding is and will continue to be a key job in manufacturing at BMA. But given the size and weight of our components, and the large number of identical welds, use of a robot has really improved our workload.” In addition, the robot considerably increases productivity: “A robot can weld a seam in about half the time it used to take us.”
How the first robot paved the way for the second
“Our experiences were positive without exception, and that was a major factor in our decision to implement a second robot from Cloos. This has been in operation in our production line for continuous and batch centrifugals since 2018”, says Benjamin Heine, who operates the second welding robot. Thanks to its manipulators, it is highly mobile and its 13 axes permit even more precise control of the welding process for centrifugal housings and frames. Overall, the second robot offers a wider range of possible applications.
Automation: BMA relies on team experience
Doreen Hennings, Senior Manager Quality Assurance at BMA and responsible for our continuous improvement process, says: “By using robots, we can make our processes leaner and more efficient, reduce the workload for our employees, and ensure a consistently high level of quality. That helps optimise production, and thus ultimately secure the future of our business site.” Hennings also thinks it is very important to actively include employees in the transformation process: “They are familiar with every detail of their job routines and can therefore make good suggestions for the automation of individual processes.”
BMA investments in automation for a strong future
BMA has been building machinery, plants and equipment for 170 years. Over the years and decades, we have continued to evolve, always striving to bring our customers in the sugar industry first-class products and services. The use of robots and automation systems is a new milestone in the history of our company. Doreen Hennings sums it up perfectly: “With the use of state-of-the-art technologies, we can secure our competitiveness and the future of our company – for another 170 years and beyond.”