In Latin America, BMA is known for its high-performance centrifugals – and we also enjoy a very good reputation thanks to our expert engineering team. On behalf of La Providencia, BMA is currently planning an increase in the cane sugar factory’s processing capacity.
Detailed engineering for cane sugar factory processing capacity increase
La Providencia in Argentina: capacity and efficiency increase planned by BMA
La Providencia cane sugar factory: capacity increase project
Our customer, the Ingenio La Providencia cane sugar factory, belongs to the Argentine Grupo Arcor. It has a processing capacity of 10,300 tpd of sugar cane. The ambitious plan is to increase this volume to 15,000 tpd within the next two years – a challenge that BMA has been only too happy to accept.
In the first step of its detailed engineering, BMA analyses a factory to identify areas where efficiency gains are possible. At La Providencia, we looked at all stations, from cane preparation to diffusion and juice purification, to evaporation and crystallisation. With our knowledge of the special features of sugar cane processing, we were able to develop an overall concept for the factory that takes into account all major success factors.
Quality and efficiency gains for the sugar factory
he next step in this engineering project will be to determine the factory’s current mass and heat balance. On that basis, the engineering team can establish where even small changes can have a huge impact, and where major changes to machines and processes are necessary.
This is followed by a list of machinery and equipment that La Providencia needs to increase its capacity, with a focus on quality, efficiency and safety. A key factor in the implementation of the project is a fixed timeline with the necessary milestones.
Partial automation for higher cane sugar factory output
For an increase of La Providencia’s processing capacity, the factory’s steam consumption will have to be reduced from about 50 to 55 percent o.c. (on cane) to around 33 to 37 percent o.c. An increase in output by around 50 percent compared to the actual figure is also planned.
Our engineering team has the solution: to reduce steam consumption, at least one falling-film evaporator and continuous pan boiling equipment are needed, while the current heat exchangers could be replaced with new, more efficient models. Partial automation of the plant is a key step to achieve the target processing capacity. And the list would not be complete without the high-performance centrifugals from BMA. BMA’s range of continuous and batch centrifugals includes special model variants for sugar from cane and beet.
La Providencia: a detailed plan for success
From an objective to the development of a concept, and to implementation planning: we handle complete projects – for new plants, plant extensions and upgrades. In the La Providencia project in Argentina BMA has developed a detailed plan together with the customer, to increase the processing capacity of the factory and at the same time lower steam consumption.
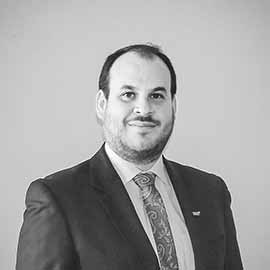