A major North American sugar producer has placed an order with BMA for manufacture of a cooling crystalliser for first seed massecuite. BMA had previously carried out a feasibility study and detailed engineering for the customer. The production of first seed massecuite in a cooling crystalliser is a tried and tested concept, made possible with equipment planned, manufactured and commissioned by BMA.
First seed massecuite – higher product quality, lower energy consumption
Cooling crystalliser from BMA for North American sugar producer
A renaissance for first seed massecuite plants
While, in the 1980s and 1990s, more than 40 plants for first seed massecuite were installed and commissioned, demand for cooling crystallisers declined after that. The European market appeared to be saturated. But for a few years now, demand has been on the rise again, particularly outside Europe. Sugar producers rely on cooling crystallisers for higher sugar quality and lower energy consumption.
In a conventional vacuum pan, there are highly supersaturated and significantly undersaturated zones. Seeding with slurry at the seeding point is particularly critical with high-purity syrup. In undersaturated zones, the slurry crystals will dissolve. In supersaturated zones, undesirable outcomes are secondary nucleation or conglomeration on the limited crystal surface of the slurry. This results in quality losses of the crystals.
Cooling crystalliser from BMA combines several benefits
In cooling crystallisers manufactured by BMA, there are no undersaturated zones. The highest possible supersaturation occurs below the fine crystal limit and does not produce conglomerates. Thanks to the even crystal size distribution, the centrifugals are more reliable in operation and need less wash water, which reduces syrup circulation.
Another benefit are far fewer losses than normal due to dust and lumps. The products have a much smaller share of sugar dust, which significantly improves the quality. It also makes drying, storage and packaging easier.
Overall, use of a cooling crystalliser to produce first seed massecuite results in lower energy consumption in the sugar house and higher product quality.
For project success: feasibility study provides all major information
BMA carried out a feasibility study to analyse use of a cooling crystalliser for first seed massecuite at the North American sugar producer’s refinery, which produces four different types of refined sugar. Achieving a higher sugar house capacity without installing an additional vacuum pan had been the customer’s specification. The objectives were to increase the sugar yield and reduce batch times in the vacuum pans.
In a first step, BMA prepared a sugar house balance for a detailed account of the current situation. The capacities of the vacuum pans and centrifugals were analysed next. This revealed that all vacuum pans were working at full capacity and that the centrifugals used a large amount of wash water.
Higher yields: seed massecuite plant for better performance
Use of a first seed massecuite plant from BMA can solve these problems, because it makes crystals with a larger crystal surface available to the vacuum pans. This reduces batch times in the vacuum pans, as well as minimising crystal aggregation and secondary nucleation. As a result, less wash water is needed.
BMA calculated three sugar house balances for use of three different feed solutions in the customer’s seed massecuite plant. They showed better performance in terms of shorter batch times and higher yields because of lower wash water use. The calculations took into account the maximum permissible colour in solution according to ICUMSA.
New seed massecuite plant: detailed engineering comprises all planning steps
As well as determining the operating ratio of the vacuum pans, BMA also analysed the centrifugal capacities in detail. On that basis, we recommended ways in which the refinery could improve centrifugal efficiency. We prepared a layout plan for implementation of the seed massecuite plant and also provided the customer with a process flow chart.
The feasibility study was followed by our detailed engineering, which included the exact integration of the cooling crystalliser and ancillary equipment in the sugar house.
Benefits speak for themselves: cooling crystalliser to be commissioned in 2023
BMA’s precise planning of the plant with all its benefits and our ready-for-implementation documentation won over the customer, who placed an order for the main equipment, specifically a cooling crystalliser and a strike receiver.
These items are currently being manufactured in the BMA workshops. Commissioning of the cooling crystalliser is expected in summer 2023.
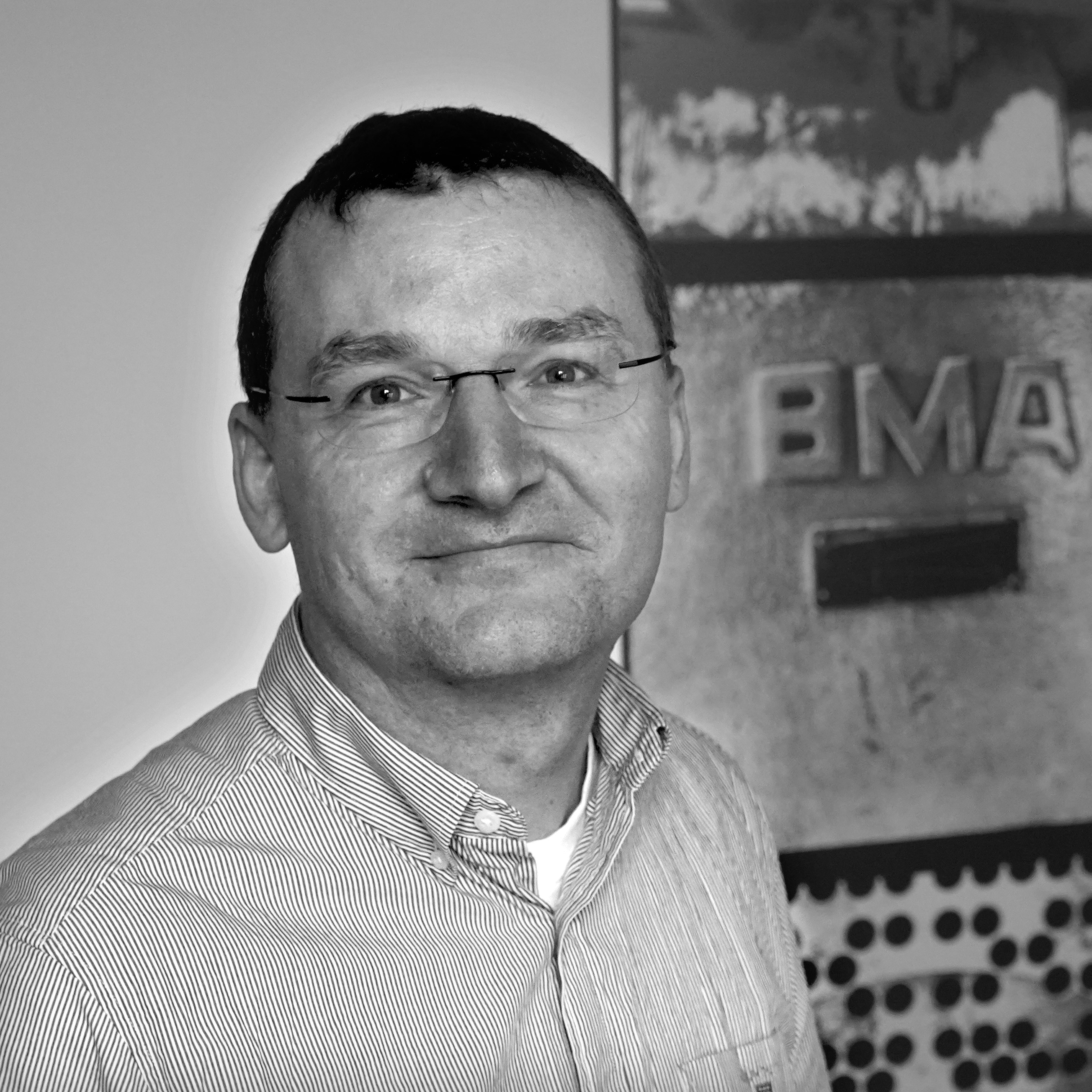